When choosing a rigging company in Houston, Texas there are many things you should consider. This article will cover the basics of rigging.
What is rigging?
Rigging is the equipment such as wire rope, turnbuckles, clevis, jacks used with cranes and other lifting equipment[1] in material handling and structure relocation. Rigging systems commonly include shackles, master links and slings. Also, lifting bags in under water lifting. Rigging Pro Houston carries a wide range of rigging and supplies.
Failing to check for simple things like the capacity of a shackle or the weight of the load are common, but preventable mistakes. Preventing mistakes—especially the common ones—is an important step in keeping your employees and facility safe.
To help gauge what some common, preventable mistakes are, we talked to some of our Lifting Specialists. Nine of the most common rigging problems they see during consultations, site visits, or inspections are:
- Weight of the load is unknown
- Not inspecting gear / not knowing what to inspect for
- Capacity of slings / hardware is unknown
- Using improperly fabricated below-the-hook devices or modified equipment
- Not using the correct sling, device, or hitch for the application
- Not using sling protection
- Not understanding the structural integrity of the load
- Failure to maintain load control
- Failure to consult rigging charts
Continue reading this article to learn more about how each of these problems might cause a mistake and how to prevent them in the first place.
1. Weight of the Load is Unknown
In order to properly lift an object to the working load limit (WLL) of the rigging equipment being used, you must know its weight. While this may sound obvious, determining the weight of the load is not always so straightforward.
It is, ultimately, the responsibility of the rigger to know the weight of the load before performing a lift. In many cases, a device that is manufactured with the expectation of being lifted frequently will have its own weight marked directly on its surface. If the weight of the load is not marked on the object, the rigger must determine the weight themselves.
Some common ways riggers determine the weight of the load are:
- Review the bill of lading or shipping documentation
- Refer to engineered prints or design plans
- Use an industrial scale, load cell, or dynamometer
- Refer to the manufacturer’s specifications or catalog data
- Calculate the weight of the load
NOTE: When calculating the total weight of the load, all rigging equipment used to rig the load should be included. This means that the weight of the slings, rigging hardware, below-the-hook lifting devices, etc. used in the lift must be calculated into the total weight lifted.
2. Not Inspecting Gear or Not Knowing What to Inspect For
Failure to regularly inspect rigging equipment for damage, defects, or deformities can lead to equipment failure and a failed lift.
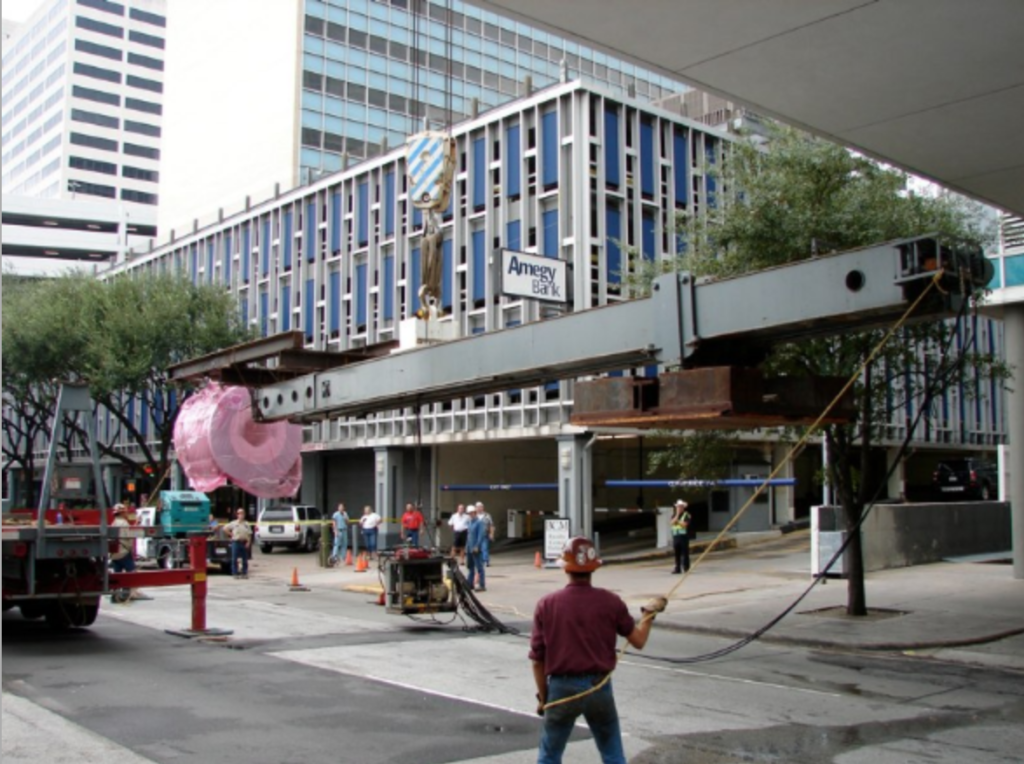
All rigging equipment and hardware must be regularly inspected. The term, Frequent Inspection, refers to the daily, or pre-shift, hands-on inspection of hardware, slings, and all fastenings and attachments.
Frequent Inspection must be performed on all equipment. For severe or special service applications, rigging equipment should be inspected before each use.
Another common problem is that, although they know to regularly inspect the equipment, the rigger does not know what exactly to inspect for during their daily inspections. In order to accurately inspect the equipment, the rigger needs to know what damaged and unsafe rigging equipment looks like.
Many facilities will hang visuals—charts, signs, or posters—throughout their shop to provide resources and reminders for acceptable and unacceptable inspection criteria. Some companies even have visual learning stations that show what bad slings, wire rope, etc. looks like.
Any employee that uses rigging equipment must have established competency for identifying damage and removal from service criteria. It is the company’s responsibility to make sure all employees are trained to the industry standard, particularly ASME B30.26 Rigging Hardware and ASME B30.9 Slings for these inspection purposes.
Periodically subjecting your employees to lifting and rigging training is a good way to keep them up to date on inspection best practices.
3. Capacity of Slings / Hardware Unknown
With a few exceptions, all rigging equipment and hardware must have the WLL clearly labeled on the device. A rigger must not use a device if the capacity is unlabeled / unknown.

A very common problem our Inspectors and Lifting Specialists run into in the field is equipment with illegible or missing tags. Without the tag, there is no way to know the capacity of the device, which is critical to performing a lift.
While devices like lifting slings require a detailed identification tag to be present, other devices like spreader bars or custom below-the-hook lifting devices require a surface label that prominently displays the rated capacity among other important information.
According to ASME, if the tag or label on any piece of rigging equipment is illegible or missing, the device must be immediately removed from service.
Some rigging equipment—eye bolts and master links, for example—will not have the WLL listed on the device but rather on a chart provided by the manufacturer. These charts must be available and accessible to the riggers as necessary—it is their responsibility to refer to the chart to determine the WLL.
4. Using Improperly Fabricated Below-the-Hook Devices or Modified Equipment
It is not uncommon for our Lifting Specialists and Inspectors to come across homemade, modified, or makeshift devices when on a site visit.
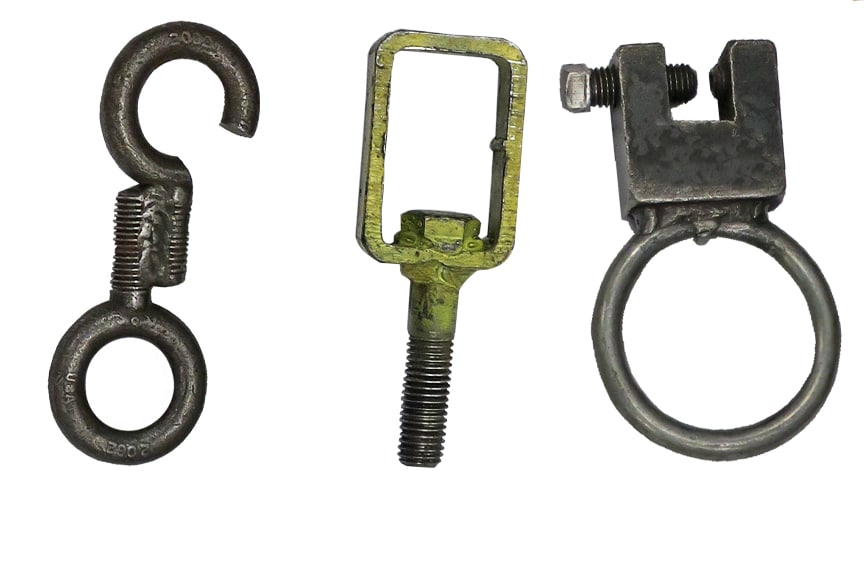
Per ASME B30.26 Rigging Hardware, modified or makeshift devices are not compliant, as it is not possible to know the WLL or Design Factor without proper load testing. This includes devices that:
- Have been made completely from scratch
- Are welded or modified in any way
- Have had parts replaced with non-OEM components
5. Not Using the Correct Sling, Device, or Hitch for the Application
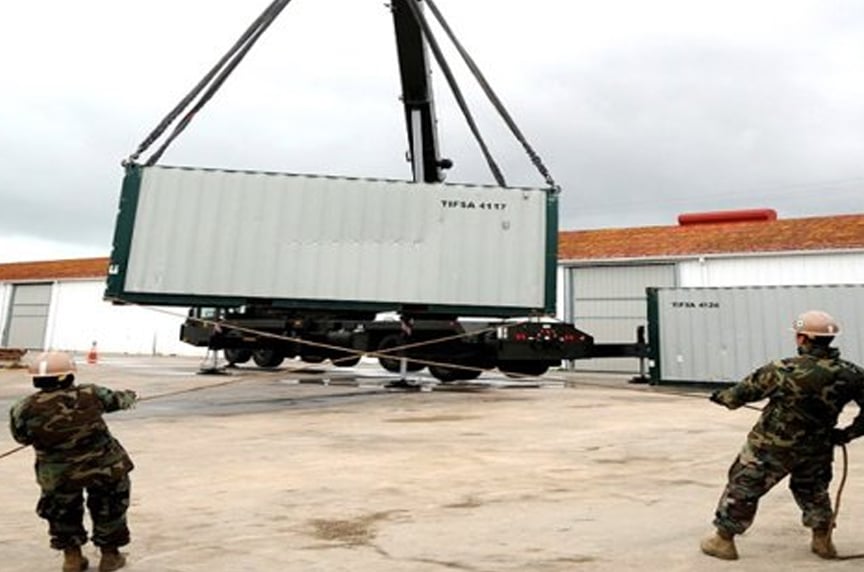
Rigging is all about planning your lift using the available equipment—slings, hardware, etc.—to make the safest, most efficient lift.
Like golf, where you have multiple clubs to choose from, rigging is not a one size fits all application. Depending on what kind of situation you are faced with, you select the appropriate rigging equipment accordingly.
One of the most common mistakes a rigger can make is not using the correct sling, device, or hitch for the lift application. While there are endless rigging scenarios, let’s go through a couple examples.
In the image shown above, using a single choker hitch was probably not the best choice as the long pipe easily slid out of the sling. If possible, a lift using a spreader beam and a double choker hitch would have likely yielded better results.
Another common mistake is choosing the wrong sling for the lifting application. For example, when using a chain sling, a choker hitch may scratch, crush, or damage the load. Slings made of a less abrasive material—nylon or polyester—would likely be a better choice for this application.
6. Not Using the Proper Sling Protection
All lifting slings need to be protected when making contact with corners, protrusions, edges, etc. Any corner must be protected against if it will make contact with a sling. Synthetic slings—web slings and roundslings— should never be used without added corner and edge protection.
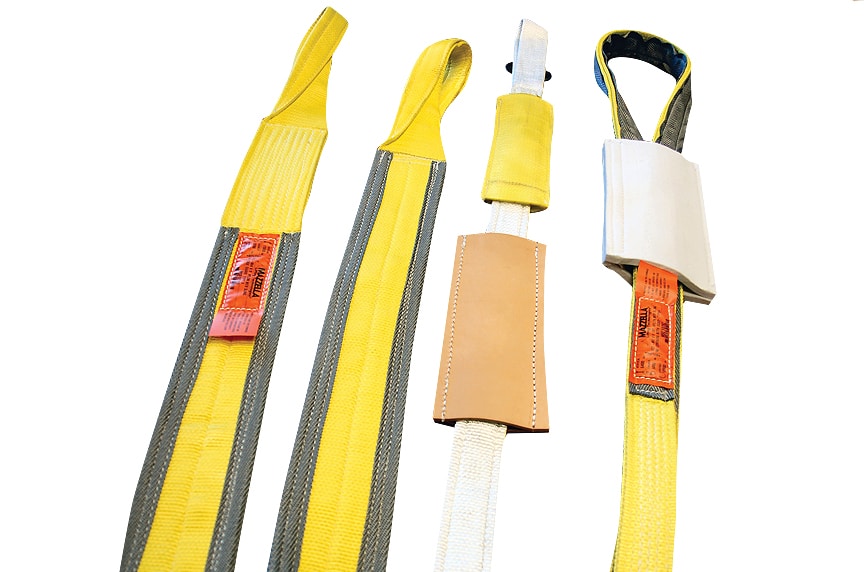
Lack of sling protection is a common rigging issue. This is especially important when using choker and basket hitches, as those types of hitches require the sling to wrap tightly around, and make direct contact with, the load.
Sling protection such as edge guards, magnetic protection, or sleeves can be added to your slings to protect them from damage. Sometimes, the sling protection can be sewn directly to the sling.
Without proper protection of lifting slings, there is a potential for:
- Injury / loss of life
- Higher turnover of slings, especially synthetic ones
- Possibility of failed lifts due to ripped and damaged slings
- More frequent damage caused to the load itself from lack of sling protection, especially when using wire rope and chain slings
7. Not Understanding the Structural Integrity of the Load
Before lifting a load, it is important to ensure that the load itself is structurally sound. This is a common problem when:
- Lifting of containers that are partially full—the contents of the container may rapidly shift to one side and cause the rigger to lose control of the load.
- The container being lifted, or the load itself, is not structurally sound. If the crate being lifted (see the image above), or the load itself, will disassemble when lifted off the ground, it is not structurally sound and will make for an unsafe lift.
A rigger must account for any contents of a load that may shift during a lift and stabilize it before the lift takes place. It’s also necessary to ensure that the load itself is structurally sound enough to be rigged and lifted from one or more lift points.
8. Failure to Maintain Load Control
There are many factors for the rigger to consider when it comes to load control. Could the wind cause the lift to go awry? Will the sling and hitch properly support and distribute the weight of the load? Are additional measures needed to ensure the load is lifted and moved along the planned path?
Failing to maintain proper load control is a common problem in rigging because, even if a load is perfectly rigged according to its weight, the lift could fail and cause serious injury and damage if not properly controlled.
Rigging and maintaining load control is a complicated process that requires careful and educated planning. In order to maintain load control, a rigger should consider these factors when planning a lift:
- Know the weight of the Load
- Determine the center of gravity
- Select the appropriate lifting and rigging equipment
- Select the appropriate sling hitch
- Be aware of possibility of fouling / clear of personnel
- Determine whether a tag line is needed
- Be aware of environmental conditions
- Understand load stabilization
9. Failure to Consult Rigging Charts
As all riggers should know, the WLL of a sling is directly dependent upon the sling hitch used in the lift, along with understanding the angle the sling is operating at.
It is not uncommon for a rigger to fail to take into account changing capacities of slings when adjusting angles or utilizing a different hitch.
As far as hitches go, the basket hitch can typically lift the most weight followed by vertical and then choker hitches.
When it comes to lifting angles, think of it in terms of your own two arms lifting two heavy buckets. If you were to hold each to your side, it would not be too difficult to handle the weight. But if you were to extend your arms straight out to your sides, that would be much more difficult—if not impossible—to manage that weight for an extended period of time. Likewise, the wider the angle of a lifting sling, the lower its capacity.
It’s very important for the rigger to take into account sling hitches and angles when determining if the equipment is capable of lifting the weight of the load. In each shop, there should be a lift guide available that breaks down WLL by:
- Sling type
- Sling size
- Hitch
- Lift angle